Understanding Porosity in Welding: Exploring Causes, Effects, and Avoidance Strategies
As professionals in the welding market are well mindful, comprehending the reasons, effects, and avoidance strategies related to porosity is critical for accomplishing durable and dependable welds. By diving right into the root triggers of porosity, analyzing its detrimental impacts on weld top quality, and exploring efficient avoidance approaches, welders can enhance their understanding and abilities to generate top quality welds constantly.
Common Reasons For Porosity
Contamination, in the kind of dirt, oil, or corrosion on the welding surface, develops gas pockets when warmed, leading to porosity in the weld. Improper protecting occurs when the protecting gas, generally utilized in procedures like MIG and TIG welding, is unable to fully shield the molten weld pool from responding with the bordering air, resulting in gas entrapment and subsequent porosity. In addition, inadequate gas protection, usually due to incorrect flow prices or nozzle positioning, can leave parts of the weld vulnerable, permitting porosity to form.
Effects on Weld Top Quality
The existence of porosity in a weld can considerably endanger the total quality and stability of the bonded joint. Porosity within a weld produces gaps or dental caries that weaken the structure, making it a lot more at risk to cracking, deterioration, and mechanical failure. These gaps work as stress concentrators, decreasing the load-bearing capability of the weld and boosting the probability of premature failing under applied stress and anxiety. Additionally, porosity can also function as potential sites for hydrogen entrapment, more exacerbating the degradation of the weld's mechanical residential properties.
Furthermore, porosity can prevent the performance of non-destructive testing (NDT) techniques, making it testing to find other problems or suspensions within the weld. This can lead to substantial security issues, especially in essential applications where the architectural integrity of the bonded elements is paramount.
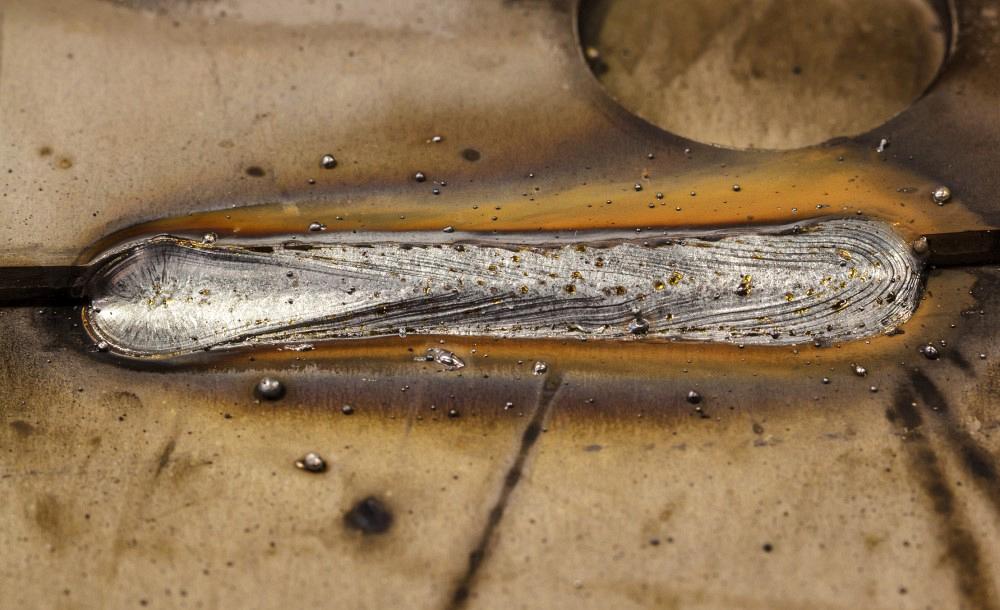
Prevention Techniques Review
Given the destructive influence of porosity on weld high quality, effective avoidance strategies are important to maintaining the structural honesty of bonded joints. Additionally, selecting the ideal welding specifications, such as voltage, current, and take a trip speed, can help minimize the threat of porosity formation. By including these prevention techniques right into welding practices, the event of porosity can be considerably reduced, leading to more powerful and more trusted welded joints.
Importance of Appropriate Protecting
Appropriate securing in welding plays an important role in stopping atmospheric contamination and making sure the honesty of bonded joints. Shielding gases, such you can try here as argon, helium, or a combination of both, are typically made use of to safeguard the weld swimming pool from responding with elements in the air like oxygen and nitrogen. When these responsive elements enter call with the hot weld pool, they can create porosity, leading to weak welds with minimized mechanical residential or commercial properties.
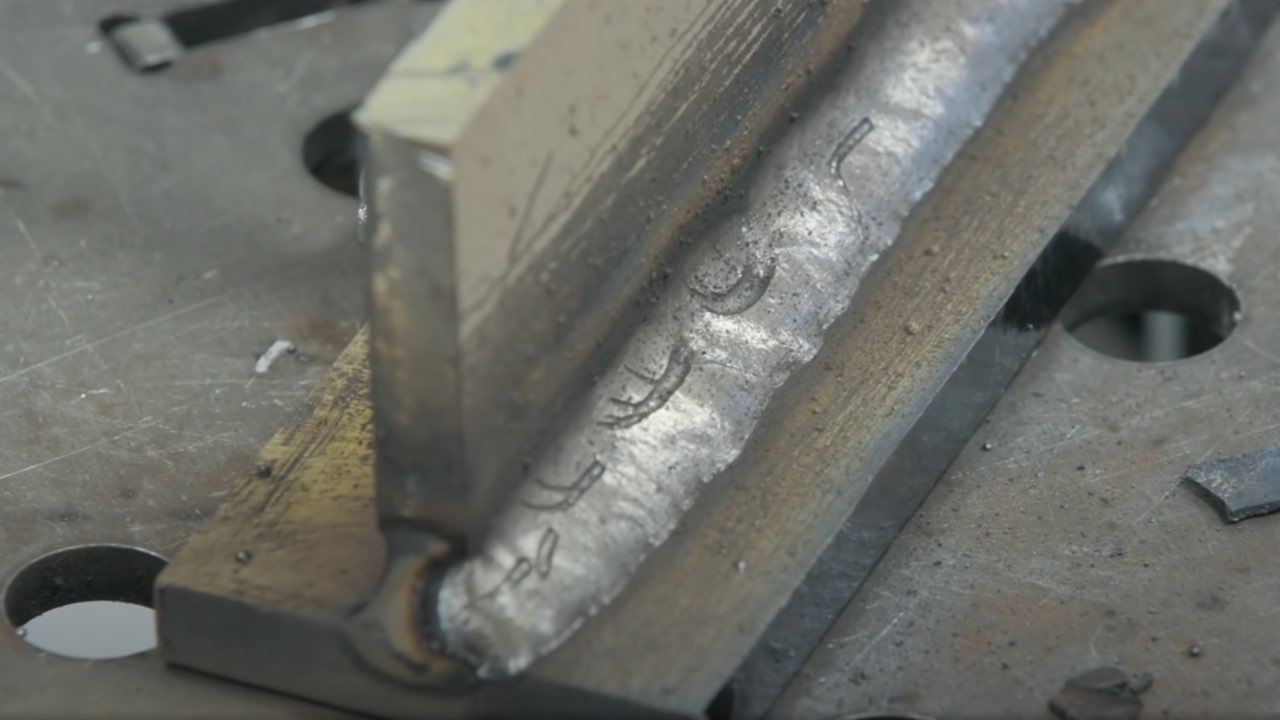
Poor securing can cause different flaws like porosity, spatter, and oxidation, jeopardizing the structural integrity of the welded joint. Visit This Link Therefore, sticking to correct protecting techniques is important to produce high-quality welds with minimal issues and make certain the durability and dependability of the welded parts (What is Porosity).
Monitoring and Control Approaches
Just how can welders effectively keep an eye on and regulate the welding process to guarantee optimum outcomes and prevent problems like porosity? By continually monitoring these variables, welders can identify variances from the excellent conditions and make immediate modifications to stop porosity development.

In addition, implementing proper training programs for welders is vital for checking and regulating the welding procedure properly. What is Porosity. Educating welders on the importance of maintaining consistent parameters, such as proper gas shielding and travel speed, can help prevent porosity issues. Regular evaluations and certifications can also make sure that welders are competent in tracking and managing welding processes
Furthermore, making use of automated welding systems can improve surveillance and control capabilities. These systems can precisely control welding specifications, decreasing the chance of human error and guaranteeing constant weld high quality. By integrating sophisticated monitoring innovations, training programs, and automated systems, welders can efficiently keep an eye on and manage the welding procedure to lessen porosity problems and achieve high-quality welds.
Conclusion
